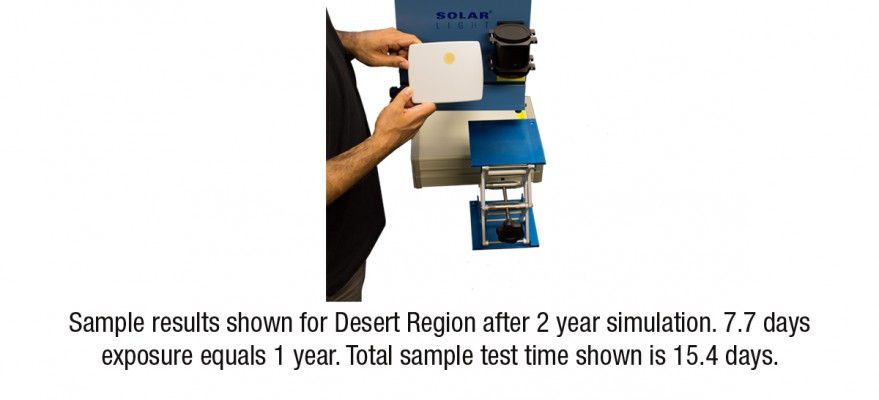
Solar Light Co. makes Solar Simulator testing kits specifically for accelerated UV plastics testing. We also have the facilities to perform accelerated UV testing at various levels of humidity and temperatures. The company’s solar simulators use a xenon arc lamp with filters and lenses to produce the entire solar UV spectrum. They generate the light to replicate the UV part of the solar spectrum without heating the sample. After plastics are exposed to the UV light, their response is used to calculate the effect that UV light would have on the plastic over years, or an average response per year of exposure.
Plastic used in construction or for various outdoor products has to hold up to the effects of sunlight for many years. The UV portion of the solar spectrum affects plastic the most, since it can break chemical bonds. The visible and IR parts of the spectrum only contribute a little to aging.
UV light can cause color changes in plastics, including the well-understood process of yellowing. It can cause plastic to lose elasticity, cause changes in its surface such as roughness or a loss of gloss, and it can produce changes in the elasticity, sealing, and transmission properties. Thus, it is important to understand how a plastic will respond to sunlight exposure before a product is subject to years of use.
In addition to the solar simulators, Solar Light makes instruments that perform light-based measurements on the plastics after UV exposure. For instance, colorimetry and photography can show color changes, and the surface gloss can be analyzed with diffuse reflectance measurements. Toughness and other mechanical properties can be measured via other means after exposure using the solar simulators.
The transmission properties of plastics are also important for applications such as the plastic lenses used with photovoltaics. It is important to understand how their transmission might change after UV exposure. Plastic films that coat replacement windows need to be tested to ensure that the films don’t delaminate and remain protective over time.
There are several reasons a manufacturer might want to do accelerated UV plastics testing. For example, if the manufacturing of a plastic part has shifted from one country to another, sometimes questions arise regarding outdoor performance. We can compare the old product with the one made in the new location. Accelerated UV exposure testing can also help pinpoint a problem with performance. For example, if the plastic product is fading fast, the company may want to add UV inhibitors. The accelerated UV testing can help the manufacture determine exactly how much UV inhibitor is needed, which is important because UV inhibitors are expensive. In this case, multiple versions of the product with different amounts of inhibitor can be analyzed.
Contact us today to find out about our UV Plastics Testing kits and services.